利用鹽酸處理爐渣獲取有價資源的再循環(huán)技術(shù)
把鋼材在酸洗過程中產(chǎn)生的廢鹽酸稀釋后,將磁選后的爐渣加入稀鹽酸溶解槽中,在pH=2-3時進(jìn)行溶解反應(yīng)。渣中除有游離CaO之外,鐵酸鈣和硅酸鈣等復(fù)合氧化物也較多,但只有Ca成分在數(shù)分鐘內(nèi)就選擇性溶解成CaCl2,而渣中Fe、Si、Mg等其他金屬 氧化物則不溶于稀鹽酸,故殘渣中Fe含量高即作為鐵源留下來。用水洗去殘渣中的氯成分后,就可用作煉鐵原料進(jìn)行再循環(huán)。
溶解試驗表明,若鹽酸濃度小于1%,渣中鈣的溶出量就少;若鹽酸濃度大于5%,除鈣以外的鐵、硅溶出量就會增多;鹽酸濃度為2%-4%時,鈣的溶出量多而鐵和硅的溶出受到抑制。
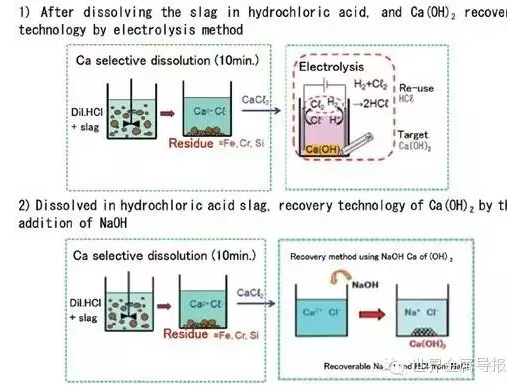
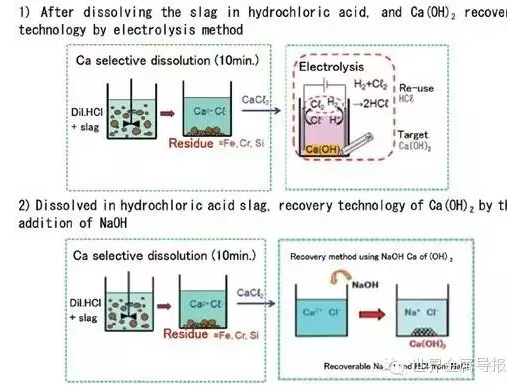
圖1 爐渣溶于稀鹽酸后的兩種Ca(OH)2回收法
如圖1上部所示,將分離出的CaCl2溶液直接電解,在陽極上產(chǎn)生Cl2,同時在陰極上生成H2和Ca(OH)2,Cl2和H2通過反應(yīng)易生成HCl,被稀釋后能反復(fù)參與爐渣的溶解反應(yīng)而被再利用。
圖1下部所示為在分離出的CaCl2溶液中加入NaOH溶液,進(jìn)行Ca(OH)2化的技術(shù)。通過加入NaOH溶液,將pH值緩慢地從酸性調(diào)整為堿性,即pH=3-4時沉淀出Fe(OH)3,pH=5-6時沉淀出Al(OH)3和Cr(OH)3,pH=8-9時沉淀出Fe(OH)2,pH=9-10時沉淀出Mn(OH)2,pH=9.5-10.5時沉淀出Mg(OH)2。故可分階段將以上沉淀物過濾后,在pH=11-13時獲得溶解性低的Ca(OH)2。再用電解處理回收Ca(OH)2后的NaCl溶液,回收NaOH和Cl2(與H2反應(yīng)為HCl),進(jìn)行再利用。此技術(shù)的特征:一是每次加入少量NaOH時,利用渣中Fe、Al、Cr、Mn、Mg的氫氧化物析出的pH區(qū)域不同,較易實現(xiàn)更細(xì)的成分分離;二是Ca(OH)2的回收率高;三是將Ca(OH)2分離后的NaCl溶液進(jìn)行電解,由于回收再利用NaOH和Cl2時的電解電壓低,基本上不能在離子滲透膜上形成附著物。
利用3.6%稀鹽酸溶解2mm以下渣粒,調(diào)查爐渣的成分選擇和溶解時間之間的關(guān)系。結(jié)果表明,10min后渣中Ca成分的溶解比例約達(dá)68%,而Ca之外的金屬僅有少量溶解。
將投入稀鹽酸中的渣粒直徑分別控制在0.125mm以下、0.250mm以下、0.500mm以下、5.00mm以下,以相同液固比和反應(yīng)時間溶解后,求出利用加入NaOH而析出Ca(OH)2的回收率。結(jié)果表明,在渣粒徑最大的0.500-5.00mm范圍,Ca(OH)2回收率低至50%-60%,但其粒徑細(xì)化到0.250mm和0.125mm時,Ca(OH)2回收率卻快速提高到70%和80%。為了避免僅因微細(xì)渣的分級對其處理量的限定,有必要在處理渣的破碎成本與Ca(OH)2回收率之間尋找最佳平衡點。
本技術(shù)分離回收的Ca(OH)2粉的粒度很細(xì),D50為20μm左右,可以推定1μm以下的實際比例達(dá)50%以上,較之市售的消石灰和生灰石,其粒度尺寸要小1-2位數(shù)。將回收的Ca(OH)2粉作為燒結(jié)黏結(jié)劑,無論是在圓盤式或是在滾筒式造球機上的成球比例都很高。